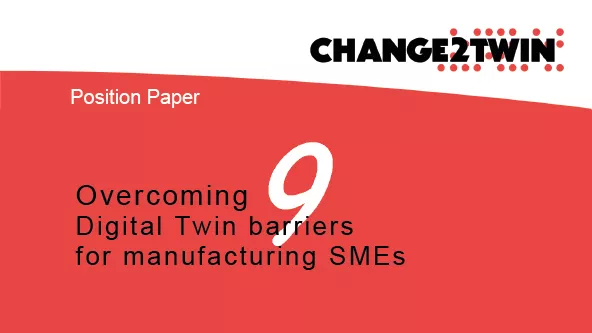
Digital twin is the trend of the hour in the industrial IoT. Many companies dream of having this digital reproduction of a product, process or production site at their disposal, due to the cost and resource saving potential it offers in the mid- to long term. However, especially SMEs often struggle with organizational and technological barriers as well as high setup costs.
“It is not surprising that companies tend to focus more on the affordability and technical complexity of the digital twin solution. But often it is a different aspect that undermines the successful adoption of a digital twin. For example, neglecting the state-of-the-art digitalisation solutions in companies leads to a digital gap and loss of competitiveness,” says Paolo Pileggi of the independent research institution TNO. Together with an international expert team, he has co-written a recent position paper for the EU-funded project Change2Twin, in which TTTech is a consortium member. The paper’s title is “Overcoming nine digital twin barriers for manufacturing SMEs” and its aim is to show enterprises how to master these nine most common barriers.
1. Lack of visionary leadership
Finding out how exactly a digital twin should improve the business is the first important step. This includes being familiar with the wide range of technologies on offer and knowing which partners can help.
2. Being unprepared for change
IoT, and digitization in general, are changing the way we work and do business. Digital twin can make industrial processes more efficient but being unprepared to make necessary organizational changes is what holds many companies back from accessing these benefits.
3. Many open questions
Digital twin opens the way not only to new technologies but also new business models. While many new choices and opportunities are exciting, they can be overwhelming, also because of barrier four below.
4. Unclear ecosystem support
There are so many digital twin purposes and specialized technologies to go with them that solutions can become complex and costly. A common language must be found via standards and best practices to make solutions more affordable and straightforward, according to Change2Twin.
5. Keeping it fit-for-purpose
Depending on its technical purpose and the business goal it was built to support, a digital twin must be updated and optimized constantly in line with that goal. However, regular maintenance and updates are often hindered by patchy system knowledge or lack of access to quality data.
6. Maintaining reliable operation
The digital twin can be used throughout the lifecycle of its “real-world” twin. While this is one of the main advantages, lifecycle management of a digital twin can be challenging because it involves a complex software and hardware system. Solutions must come with regular patches and updates.
7. Ensuring effective execution
A digital twin requires substantial computational resources. It must be clearly defined what needs to be done at the edge of the system, for example via an edge computing platform like TTTech Industrial’s Nerve, and what is done in a cloud computing environment. In the case of Nerve Blue, even the exchange and data flow between edge and cloud can be dealt with efficiently and flexibly.
8. Accounting for uncertainty
Good data is the basis of good digital twin solutions. Data, as well as simulation and reasoning models need to be understood and trusted thoroughly before going into use.
9. Bringing it all together
Developing a digital twin requires understanding of the dynamics of the whole system. It involves bringing data from several sources together into the homogeneous data format of a digital twin. An open and vendor-independent platform like Nerve Blue can host any data manipulation tool or even combine all your needed applications to handle and correlate your data.
Regardless of these challenges, digitizing your manufacturing business is worth it in the long run. In Change2Twin, Europe is building a community designed to help SMEs overcome these barriers to take European manufacturing to the next, more digital, level. TTTech Industrial is on board, too and supports the project with its industrial edge computing platform Nerve Blue.
You can find out more about these challenges and how to overcome them in the Change2Twin position paper. Whether you are an SME, a technology provider, consultant or digitalization stakeholder, you are sure to find the contents useful.