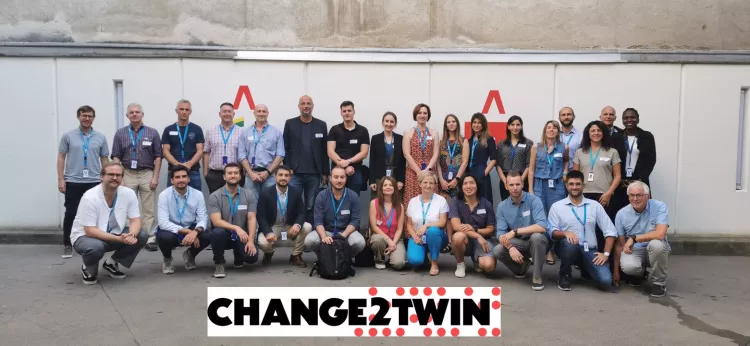
Digitalization is one of modern manufacturing’s greatest challenges. While some businesses are already very far along in their digitalization journey, some are still at the start. However, every business will eventually have to tackle digitalization to stay competitive in almost any market.
One of the most promising trends for manufacturing businesses is the digital twin. A digital twin is a digital reproduction of a physical object – like a product, a machine, or even a complete production plant. It is a game-changer for many industries because it makes it possible to make decisions based on digital models, rather than waste time and resources on experimentation and prototyping in the physical world.
What sounds great in principle can be hard to do in practice, especially for smaller companies with limited budgets and staff resources. “There is no standard digital twin solution that fits everyone,” says Dr. Francesca Flamigni, Innovation Projects & Funding Manager at TTTech. “A digital twin is a perfect duplicate of its physical counterpart, and just as unique. Even the technologies you choose to create your digital twin will be dependent on your use case.”
A digital learning journey
Francesca is the technical project manager for Change2Twin, a European project that provides funding and mentoring for SMEs on the way to their first digital twin. Beneficiaries of the program, who had qualified for the so-called “Deployment Voucher” (a 90,000 euro funding, plus technical mentorship) met in Vienna last month to introduce the digital twin projects, on which they would be working in the upcoming months, together with their dedicated mentors. For Francesca, it is already her second tenure as a mentor: “We have learned a lot from our first round of Deployment Voucher beneficiaries that can really help our second group,” she says. “Even us mentors are learning a lot about what can be done with a digital twin. The possibilities we see are endless.”
What exactly can be done with a digital twin? Here are only some of the many inventive and exciting digital twin use cases that made the cut for the 2023 Deployment Voucher:
Increased efficiency and better customer service with a digital twin
Labormak S.r.l, located in Northern Italy, is a company that deals with the electro-chemical treatment of aluminum foils. Their decision to implement a digital twin was based on an objective to improve the possibility of closing deals with customers by 15%, providing a better understanding of the proposed plant and improving efficiency by saving 40% of commissioning time. The goal is the realization of intralogistics automatic lines to handle different types of parcels, especially dedicated to customers acting as mass distribution centers of food and beverage products. In its pilot, Labormark aims to use TTTech Industrial’s Nerve, an IIoT platform that is listed in the Change2Twin Marketplace as one of the possible enabling technologies for a digital twin.
Listen to Federico Fumagalli of Labormak explain their planned solution:
Digital twin to reduce food waste and improve quality
MIRELITE MIRSA Zrt. is a Hungarian family business engaged in the production of various quick-frozen vegetables, fruits, and pasta. Although the product manufacturing and packaging are already done with modern technologies and machines, the company decided to apply for the Deployment Voucher to improve their vegetable blancher. They realize that digitalization and the use of digital twins for dynamically synchronizing the heating and chilling with the mass flow will optimize resource efficiency, reduce energy, and water consumption, reduce the cost and waste of food, and improve food safety and quality.
Digital Twin for Mirelite Mirsa: interview with Gergely Boromisza:
AI-based monitoring of eco-friendliness in textile production
Stotex doo is a Serbian textile manufacturing company. They want to implement a digital twin to gain a zero-waste and a zero-defect production process. Their goal is to achieve eco-friendly production through RETROFITT's existing textile processing machines using AI and digital twins, which allows them to monitor the dynamics of the production system and predict its behavior in a digital environment. Ultimately, the company’s mission is to become a leader in socially responsible trading and manufacturing.
15 beneficiaries in total presented their planned projects in Vienna, all of them equally exciting – we have barely scratched the surface. Head to the Change2Twin YouTube channel to look at interviews with the beneficiaries and find out about their digital twin plans.